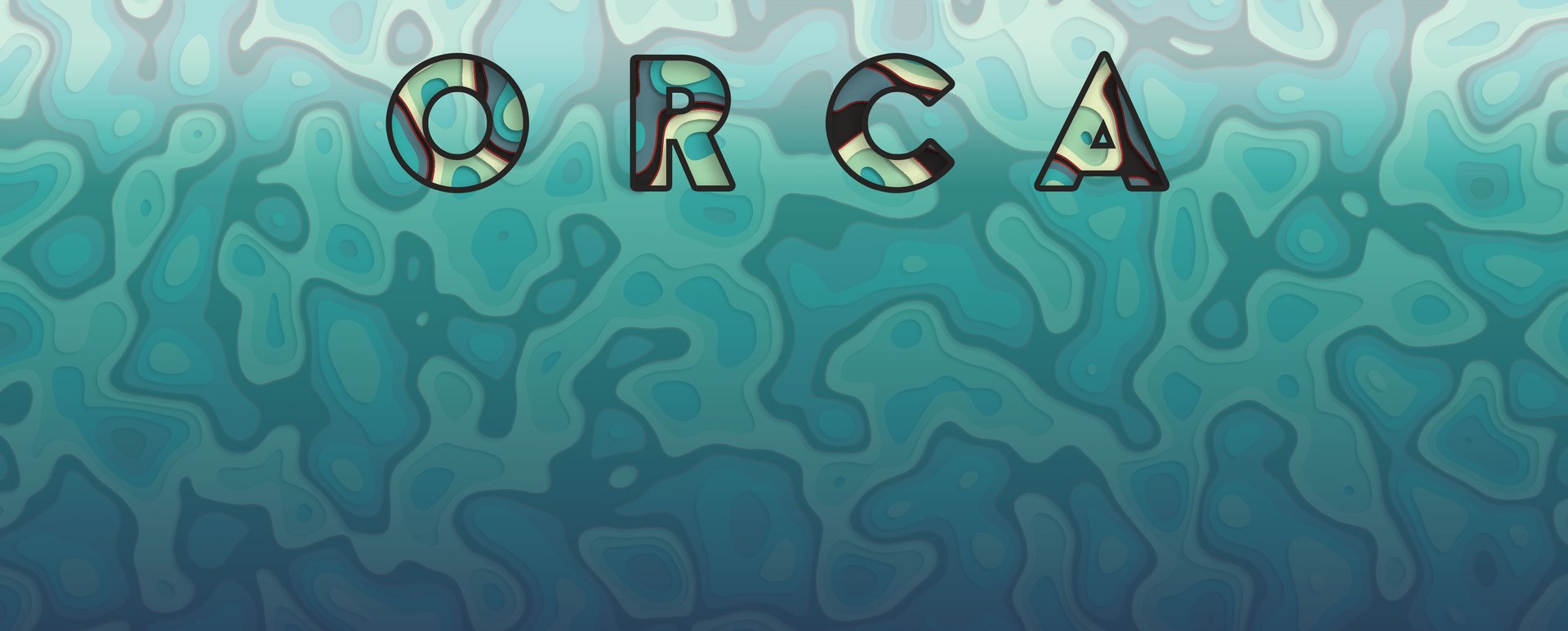
"Make a custom fit piece of cutlery" Kitchen knife is cutlery right? Yeahhh.
Great project. Tons of fun. Just wish it would not need to be custom fitted to my hand. Makes it look derpy. So my wish is to redesign the handle and make the knife out of proper knife steel. Have it CNC milled instead of water cut and create something usable. Oh baby. exciting.
Below here you'll find heaps of pictures though the process along with the steps. All I will do before Ill slave away over another glorious video.
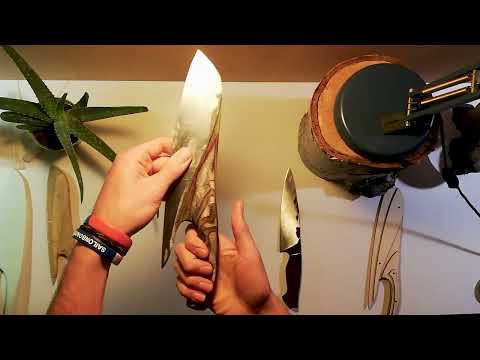
Sales pitch
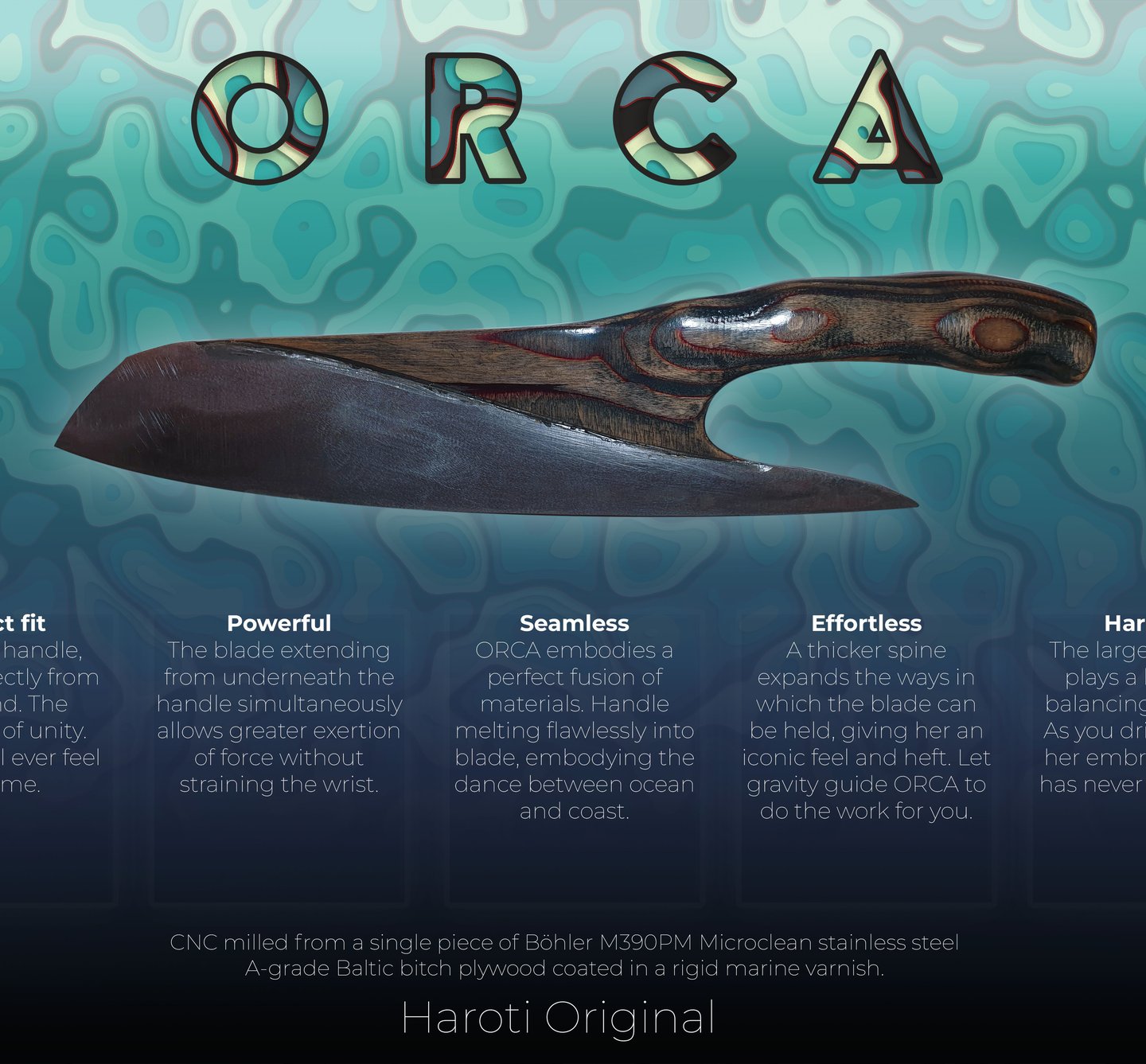
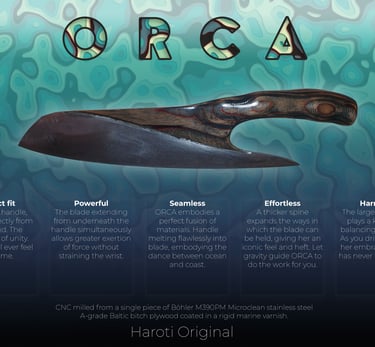
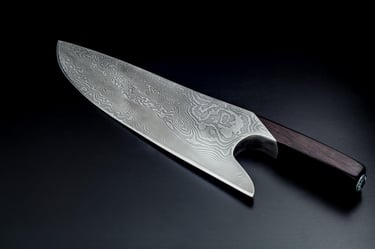

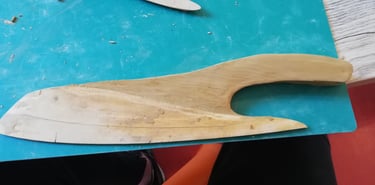
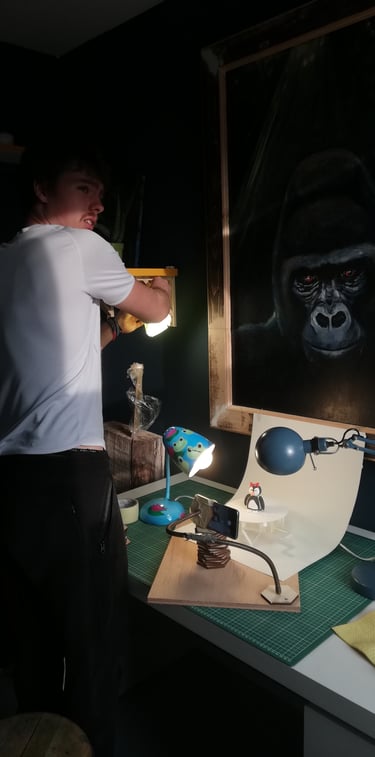

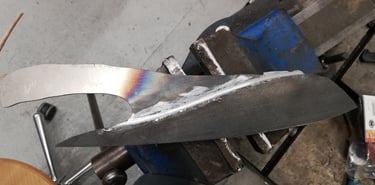
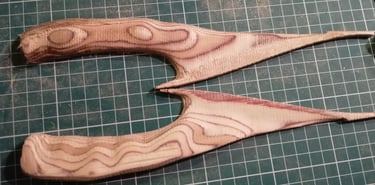
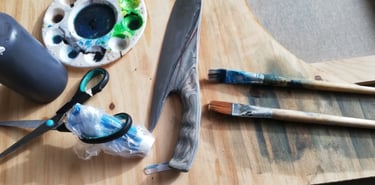

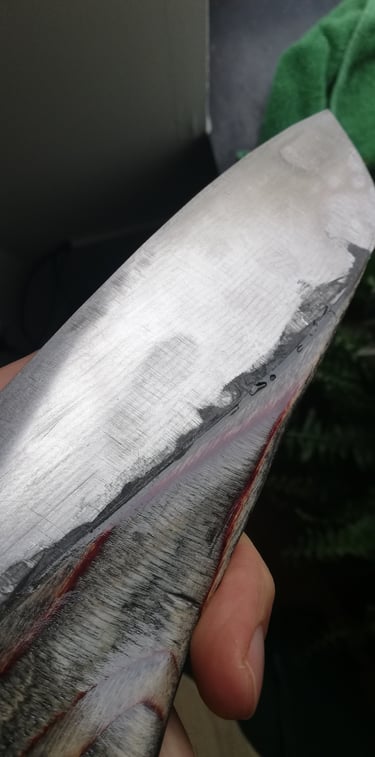
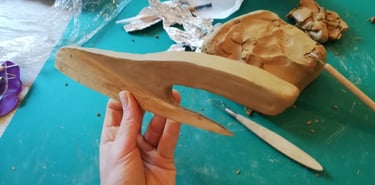
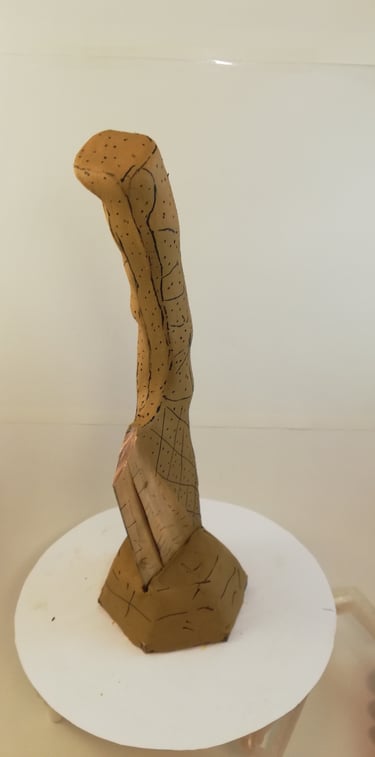
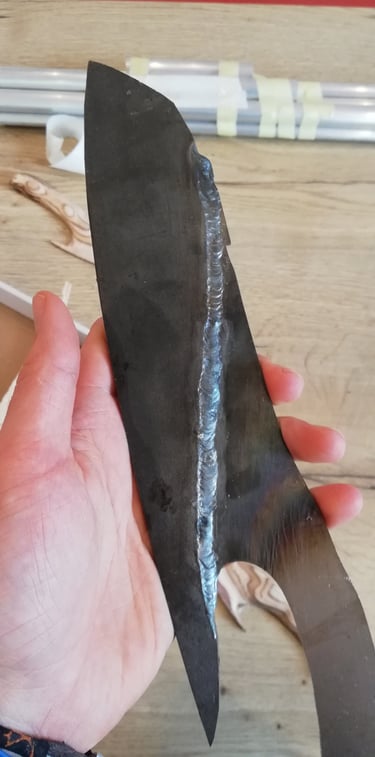
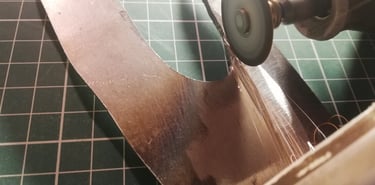
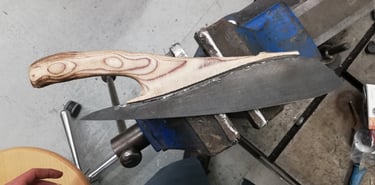
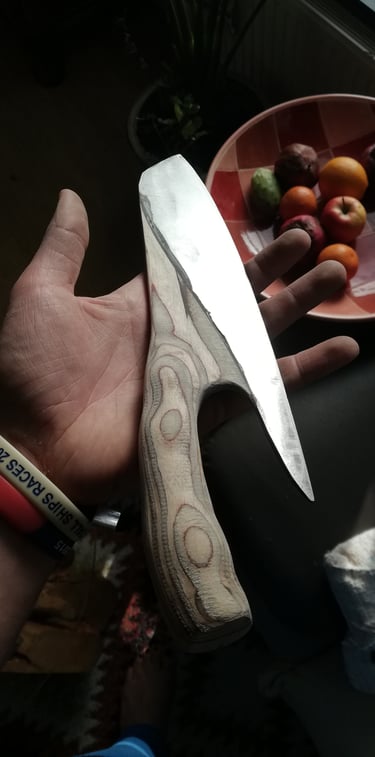
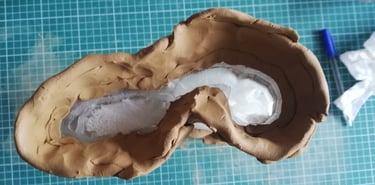
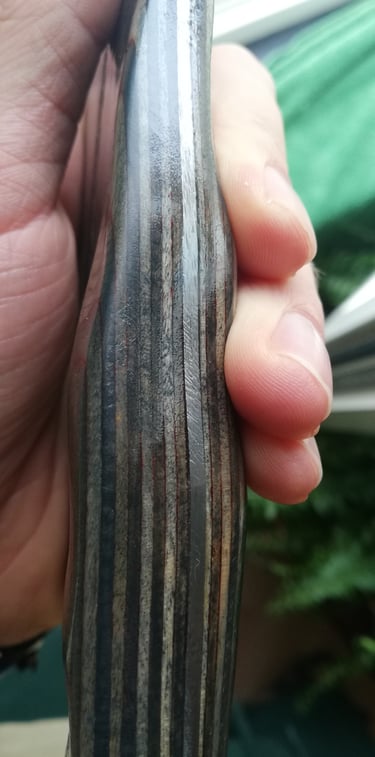
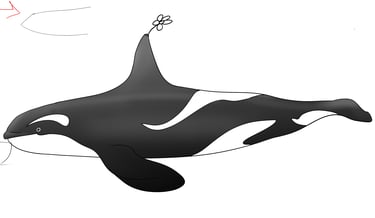
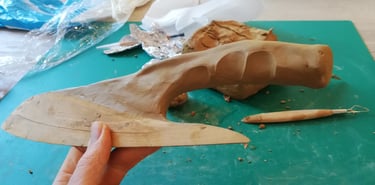
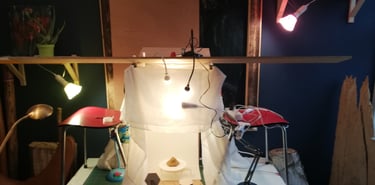
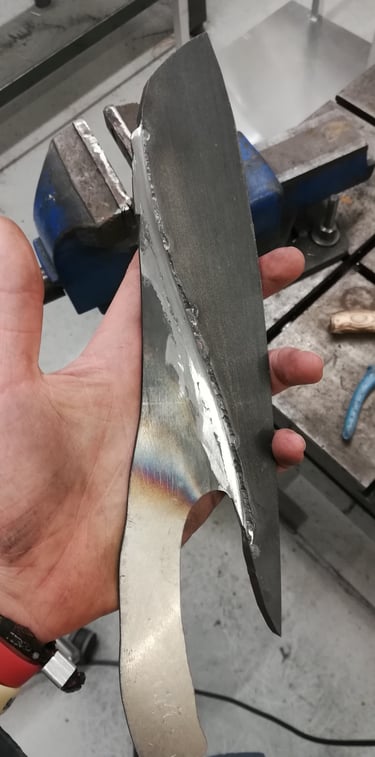
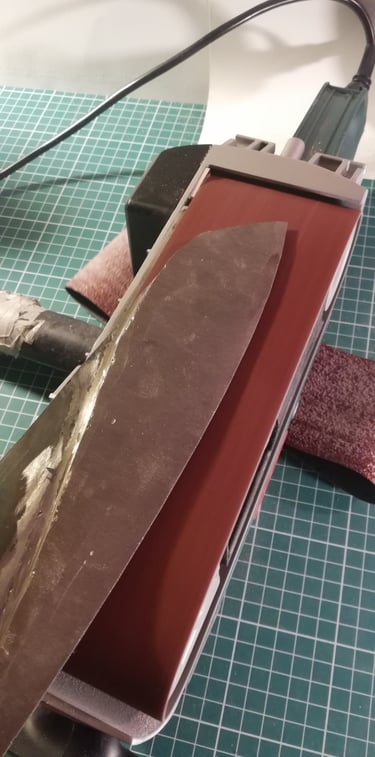
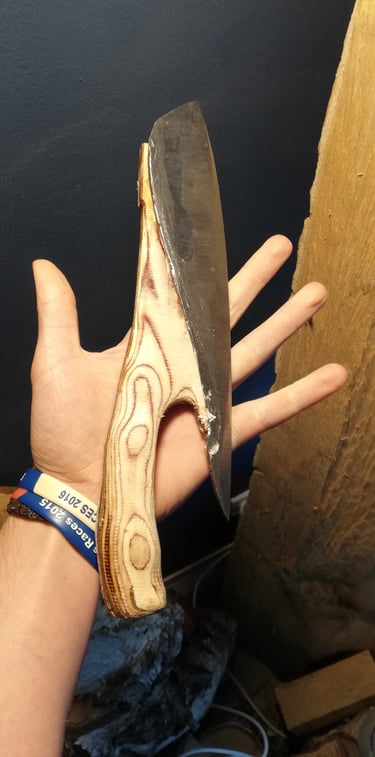
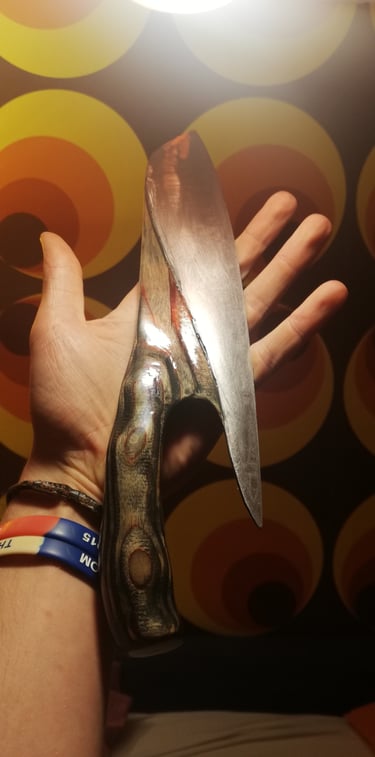
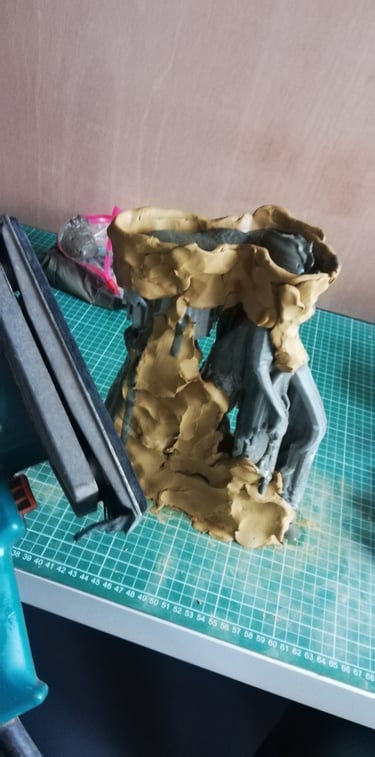
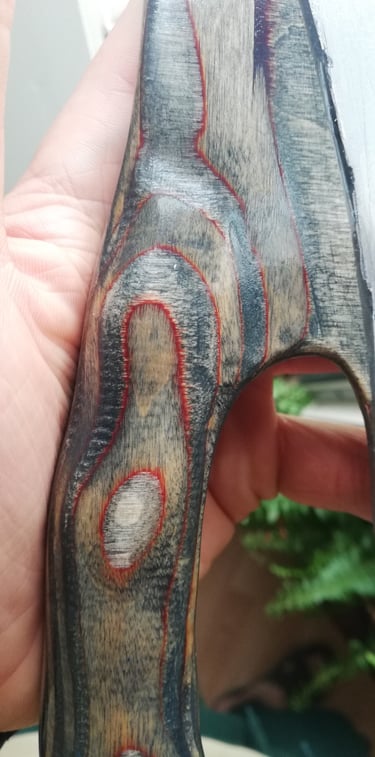
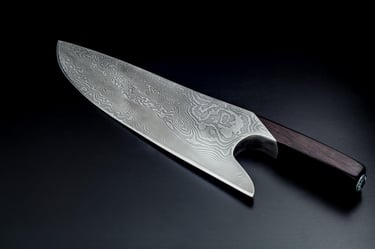

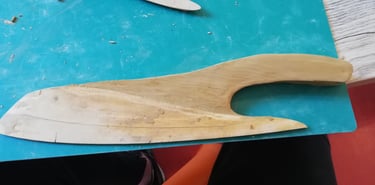
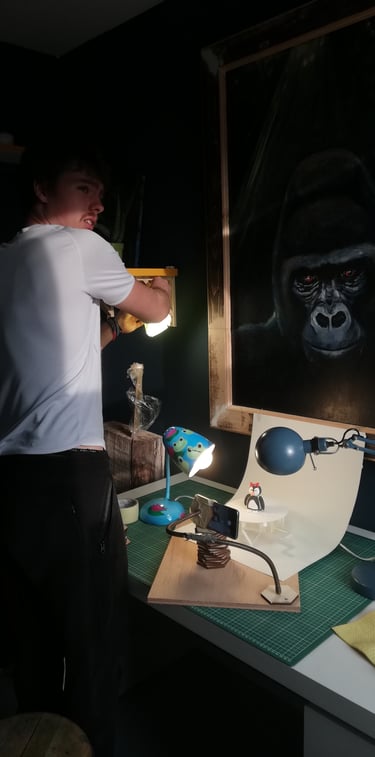

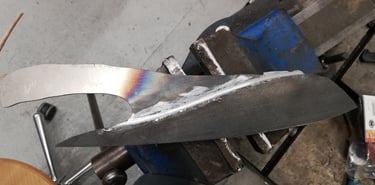
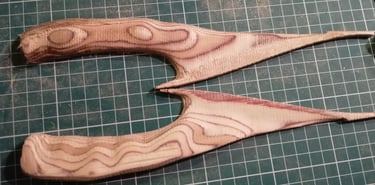
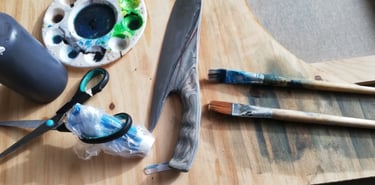

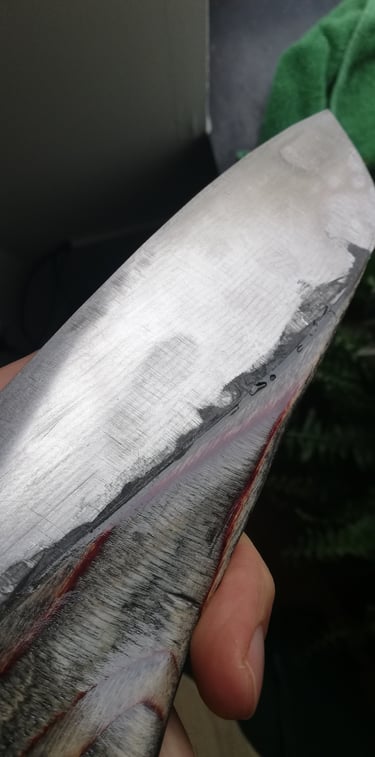
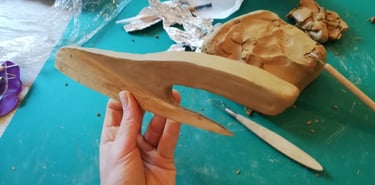
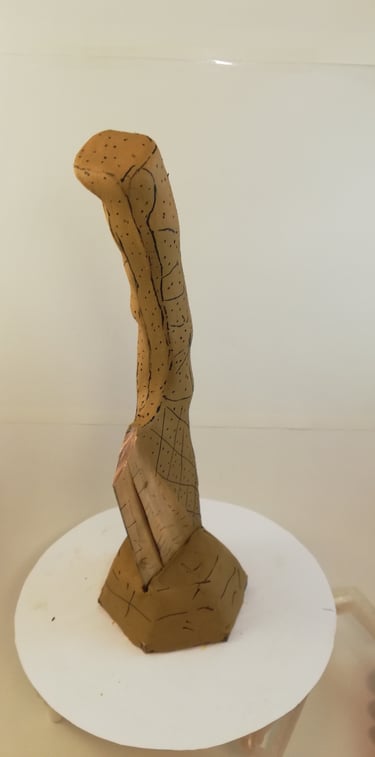
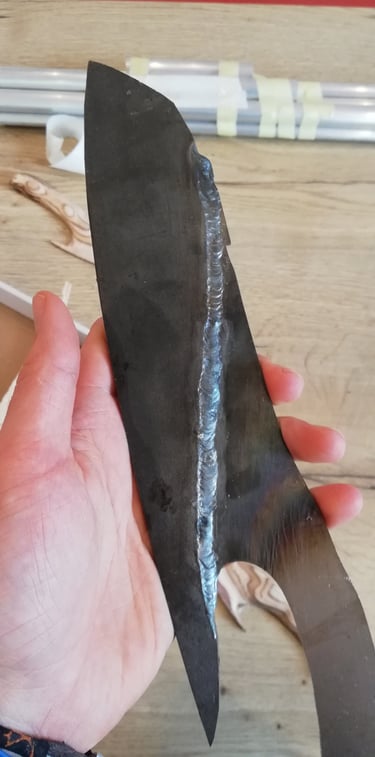
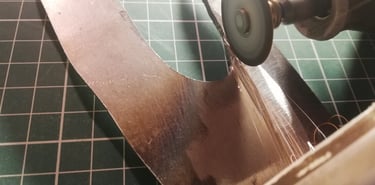
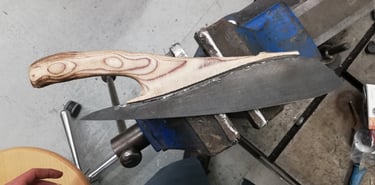
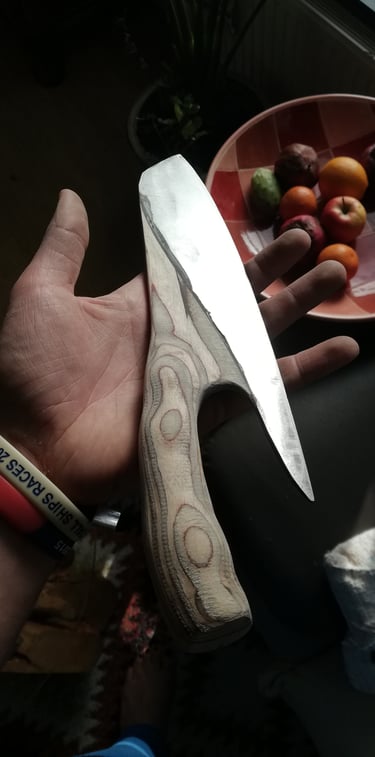
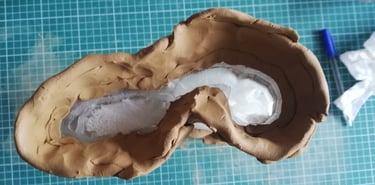
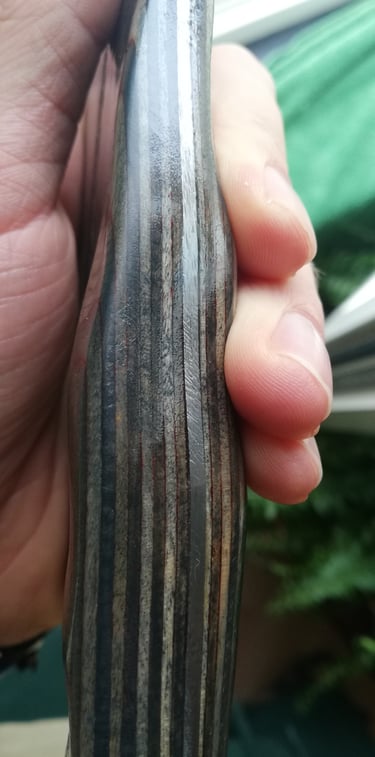
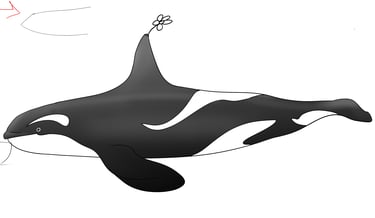
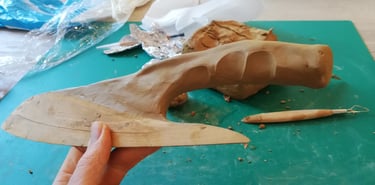
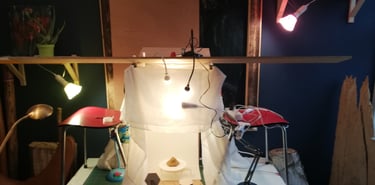
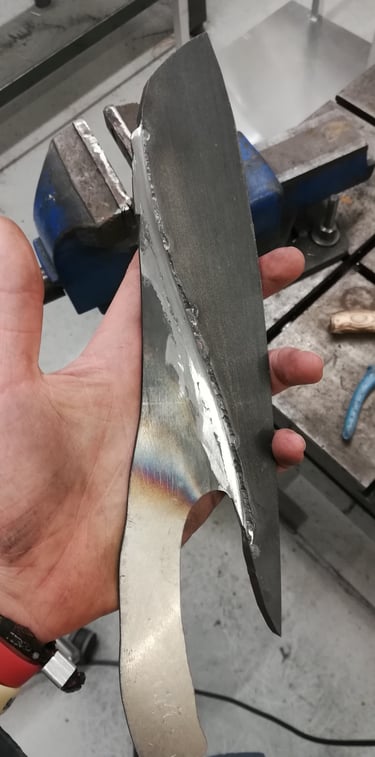
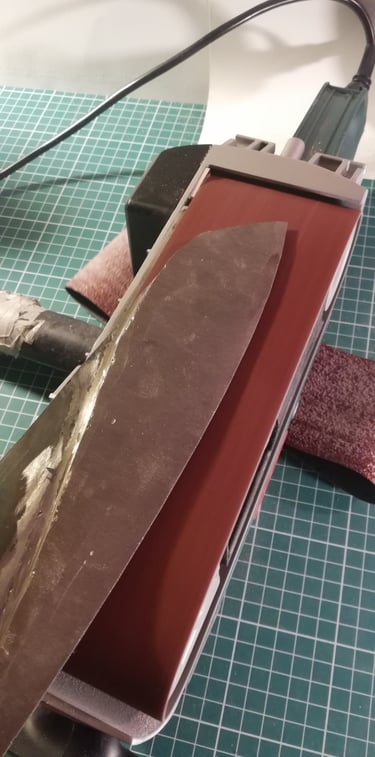
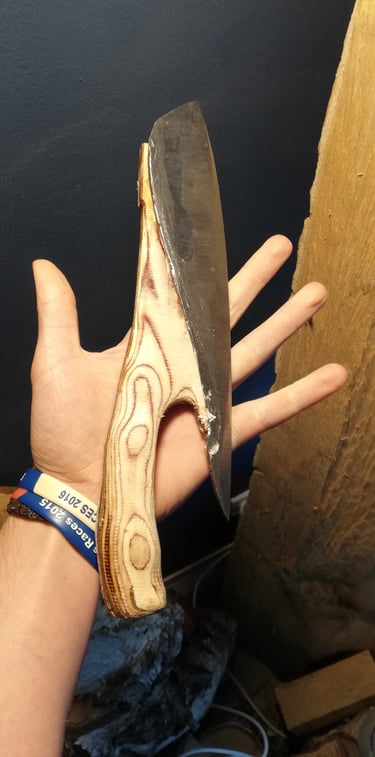
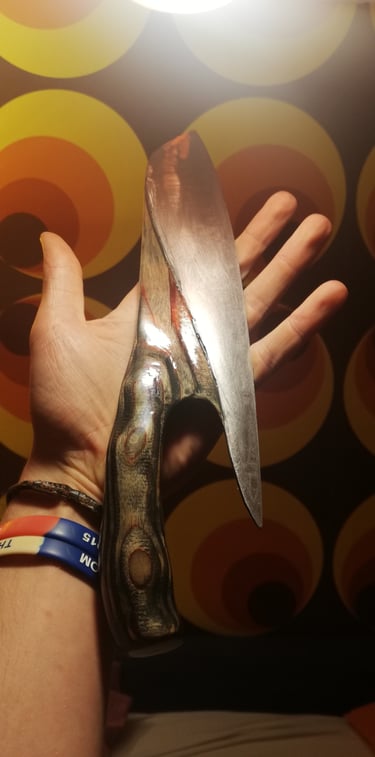
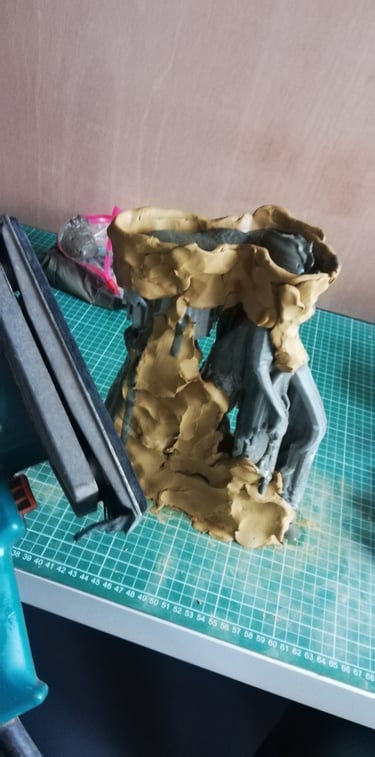
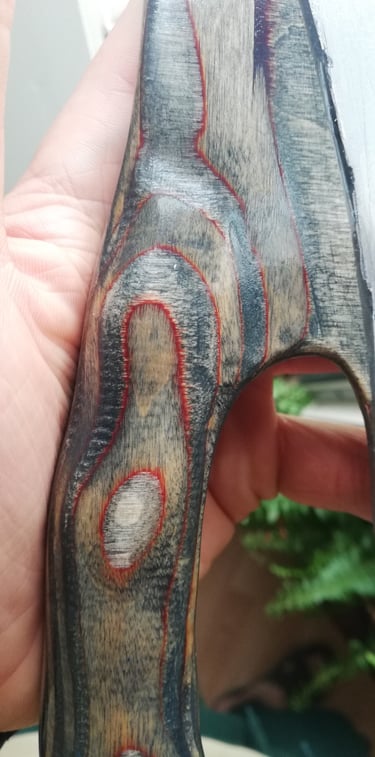
Draw out an idea for the wood to be laser cut
Refine the idea into a design in photoshop
Copy the plan photoshop using the pen tool.
Convert to a sketch in Solidworks and extrude out different pieces.
Exporting to illustrator and export to DXF
Lasercut the shapes.
Play around with The Great Wave off Kanagawa and the golden ratio for the knife holder
Decide that you want more and laser cut different sizes
Choose the one with the best fit and model over with clay
Model the handle onto it with clay
Have a great model but forget to water it and have it crack.
Make a model with two thicknesses in Solidworks
Realize this has to be made from two separate pieces of metal
Split previous Solidworks model into a 2 part design (because CNC milling from one piece is not possible)
Start a new model and keep it wet moist this time
Write a grasshopper script that merges the handle scan and Solidworks model and split into three pieces
Try to scan the model at the TU
Bertus is not there so you’ll have to build yourself a scanner
Build a DIY photogrammetry setup with which to scan the handle
Make a test scan with a clay penguin
Realize you need more lights
Attempt to scan the knife and get shitty results
Cut of the tail and tip of the knife and add markers to it, also, add all the lights in the house
Scan the handle (492 scans)
Smooth the model in zephyr
Fix the model in blender
Merge with the Solidworks model
Split into three parts
Convert middle part to SVG file for water cutting
Add water cutting tabs to thin and thick metal piece
Spend a whole day exporting the two handle pieces to step files
Learn that the max # of vertices is 15k and that 9.8M really is too much
Export to step
Send all files to PMB and let them to their magic
Work on knife holder
Realize your knife holder idea won’t work and walk outside waiting for a new idea
Realize objects moving through water leave a wake. Make a 3d model turn into a virtual knife holder
Write grasshopper script that slices the model and make ready for laser cutter
Realize that 131 slices are too much to cut
Reiterate the model to lower the # of slices.
Run out of time to cut and think of a new idea again
Get the knife back from PMB
See you should have been more specific in what you wanted
Spend all day grinding away the weld and sharpening the knife
Realize 8mm is way too thick for steel. Thinner is possible. Real knife steel is possible now as well.
Ask questions and learn that they can CNC the blade saving hours of works and better result
Sand the handles and glue them to the knife
Paint the handle
But dry it with heat gun quickly so the multiplex doesn’t start to peel
Coat handle in 7 layers of spray on lacquer
Combine three support in cure and the way the knife was lodged in clay when scanned
(Should have only added support from ground up. More removal work)
Design and print the new knife holder
Fill the print with cement